Centralized ink control
Laser anilox roll cleaning system
I-ICS centralized ink control system
Total optimization of ink control in flexo and gravure printing. Accuracy, efficiency and ease of use.
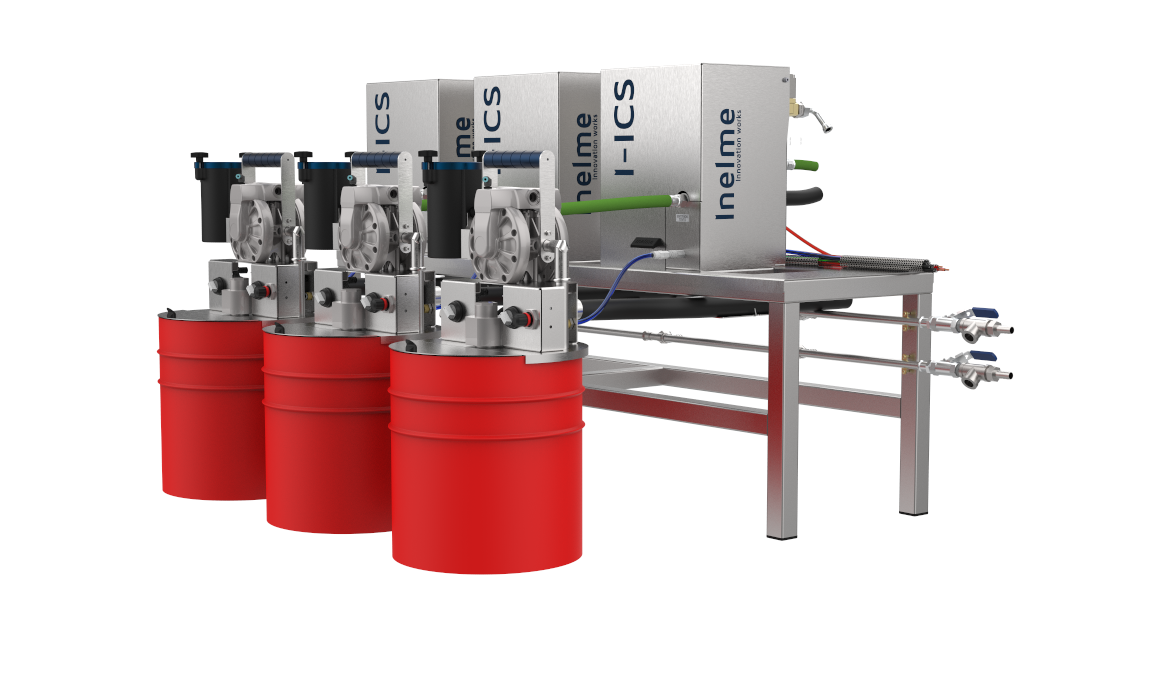
Contact us today and find out how I-ICS can revolutionize your printing process.
Advantages of I-ICS centralized ink control system
The I-SSS-TT transport cart is designed to facilitate the handling and transport of anilox sleeves with an outer diameter of up to 200 mm. With a capacity of 16 sleeves, this cart can be customized in height to suit specific roll needs.
Rugged materials: Constructed with durable materials that ensure longevity in any production environment. User-friendly casters: Equipped with casters for effortless and agile transport. Compatibility: Perfectly complements our Anilox and Sleeve Storage System (I-SSS), a vertical, modular storage system designed to maximize space and protect anilox sleeves from damage.
Benefit from all the advantages of our I-LAC machines
Give us your contact information and receive professional advice without obligation.
Up to 80% time savings when cleaning Anilox cylinders with I-Lac machines
Cleaning anilox cylinders has always been one of the biggest concerns for flexo printers. If the cylinders are not perfectly clean, their transfer capacity is reduced and therefore the color intensity of the print is lost, with the consequences for the production that this can have: invalid prints, longer start-up times, etc. I-LAC solves this problem effectively thanks to the laser that removes the dried ink from the inside of the cells without damaging the cylinder cells. A specially designed optical laser vaporizes any residue and cleans away dried ink, adhesives, waxes, silicones, etc. Laser technology allows cleaning without exerting any mechanical or thermal action on the anilox cylinder, which allows us to clean even after each use and preserve the useful life of the anilox rollers for much longer.
We have I-LAC machines with measurements from 500 mm in length to 3500 mm (cylinder without shafts), and special measurements can be adapted according to needs.
Model |
Maximum cleaning length (cylinder without shafts): |
Minimum cylinder diameter: |
Maximum cylinder diameter: |
I-LAC F60- 6 |
600 mm |
Ø55 mm |
Ø200 mm |
I-LAC F60 – 10 |
1000 mm |
Ø110 mm |
Ø300 mm |
I-LAC F60 – 15 |
1500 mm |
Ø110 mm |
Ø300 mm |
I-LAC F60 – 20 |
2000 mm |
Ø110 mm |
Ø300 mm |
I-LAC F60 – 25 |
2500 mm |
Ø110 mm |
Ø300 mm |
I-LAC F60 – 30 |
3000 mm |
Ø110 mm |
Ø300 mm |
I-LAC F60 – 35 |
3500 mm |
Ø110 mm |
Ø300 mm |
Receive in your email the dossier with the complete technical information
INK CONTROL SYSTEM
Solutions for the Flexographic and Rotogravure Professional
Our Ink Control System (I-ICS) controls the most important parameters of flexo and gravure inks. Pigment concentration, viscosity, pH and temperature are measured by means of sensors and automatically regulated, thus guaranteeing color reproduction with minimal tonal variations throughout the print run and, by memorizing the working conditions, drastically reducing color adjustment times by reproducing the same printed tone in the following repetitions. I-ICS is a centralized control system for flexographic and gravure printing presses that adapts to any printer and number of printing stations (colors) on the market, and comes with multiple installation options in terms of cabinets, supports or adaptations to different machines. It is controlled by a very intuitive software on a touch screen monitor with which you can manage the current working conditions such as color labels, concentration, temperature, pH, solvent formulas used to maintain viscosity or clean, evolution graphs and a job history to reuse them whenever you want.
SAME TONE PRINTED THROUGHOUT THE WORK
REDUCES COLOR ADJUSTMENT TIMES IN REPETITIONS
OPTIONS AVAILABLE FOR AUTOMATIC WASHING, REFILLING, CONSUMPTION CALCULATION AND CUSTOMIZED DESIGNS
DATA COLLECTION AND MEASUREMENTS OF TEMPERATURE AND VISCOSITY FOR USE IN FUTURE WORK
INTUITIVE AND VERY EASY TO USE
SERIES INTEGRATION WITH THE INK DRIVE LINE
CAN BE UPGRADED AFTER THE FIRST INSTALLATION BY ADDING NEW EXISTING FEATURES OR FUTURE DEVELOPMENTS
CONFIGURABLE FOR ANY FLEXO, GRAVURE, GRAVURE, CARTON OR SPECIAL APPLICATION PRINTER MODEL
FEATURES OF OUR INK CONTROL SYSTEM
Concentration control - viscosity
Considering the viscosity and temperature variables, our color control module maintains a constant concentration corresponding to the ratio between pigment + resin and solvent/water. The system is able to compensate for viscosity variations caused by temperature changes. Viscosity is constantly measured by measuring the falling time of a body inside a tube through which the ink flows. In addition, the measuring unit incorporates a probe for continuous temperature measurement. The viscosity and temperature data are sent to the computer where they are interpreted to calculate the ink concentration in %. This system measures more accurately than other viscometers based on the measurement of ultrasonic technologies, cups, pressure variation, etc...
Temperature Control
- Improved print quality results by decreasing dot gain in color selections and improving the outline in spot colors.
- Drying control, in solvent base the ink does not dry on the plate and is transferred to the printed substrate with better outline and intensity. In water base the ink is more stable as it avoids pH variations due to evaporation.
- Prevents water absorption by ink hydroscopy, resulting in brighter colors.
- Significant solvent savings by avoiding evaporation and achieving a stable concentration.
Solvent mixer
It allows you to create formulas for up to 4 different solvents to prepare, on-line, the dilution solvent for color control and cleaning used individually at each printing station. The formulas are associated with each printing station and are saved in the job sheet for future repetitions. In this way, inks of different technologies can be used, as well as adjusting the formula of the solvent used based on the temperature, ambient humidity or printing speed.
Solvent Consumption
It quantifies the solvent consumed at each printing station, using flow sensors, distinguishing between whether it is used for washing or viscosity control, and provides reports on the quantity of solvent used in a given period of time or in a given job. It presents the result in graphs and reports. With this consumption measurement system, the production costs of each job can be known and forecasts can be made for solvent purchases.
PH control for water-based ink
It is a pH control module that far exceeds market standards in its field of action. It is intended for water-based inks, and automatically measures and corrects the pH levels of the ink used, keeping all the qualities of the ink stable. It is made up of sensors, one for each measurement unit, controlled by software and with a pH correction addition valve. pH control in water-based inks allows drying to be adjusted. Lowering the pH level results in quick-drying inks and thanks to automatic control, the risk of defective prints due to inks with pH levels that are too low is eliminated, since the tendency of an ink in production is to lose pH level.
Magnetic ink filters
Filters with magnets are incorporated into the ink inlet line to remove impurities that may damage both the control and printing systems. The magnets remove metallic particles that normally come from the blades of the printing body. There are different filter mesh pitches, in addition, the filter body acts as an expansion vessel in pneumatic pump circuits, minimizing the water hammer caused by these. During printing, all kinds of solid waste fall into the ink. The filters prevent these particles from passing through the circuit, avoiding printing defects, scratches on the chrome plated rotogravure cylinders or on the flexographic anilox, obstructions of the alveoli of these same cylinders or deposits in pipes and ink pumps. Available with different configurations and thread pitches.
Agitators to eliminate foam and mix the solvent or water with the ink
The agitators are presented as another module of the I-ICS system and improve the mixture between ink and solvent, reduce the foam that can be generated in the ink container, minimizing the adverse effects that this can cause in the printed matter. It is installed on a stainless steel support and is activated with automatic start and stop, from the system's desk. It is also available as an independent pumping, agitation and filtering system. It can be configured with different inlet, outlet and thread pitch arrangements.
Integration and optional features
The I-ICS ink control system can be integrated with our other systems in a single control panel. There are automatic washing systems for flexographic and gravure machines, automatic ink tank refilling systems, ink consumption calculation systems or any other special functionality that can be custom developed according to customer specifications.
MULTIPLE COMBINATION POSSIBILITIES
All I-ICS modules: Ink control, temperature control, Agitators, Solvent consumption measurement, pH control, independent solvent mixing and magnetic ink filters, are designed to be added to the printing equipment under the same chassis and in the same control panel.
Both water-based and solvent-based inks can be used:
In the case of solvent inks, these two modules can be added:
And for water-based inks we have an exclusive module:
I-ICS CAN BE COMPLEMENTED WITH I-ACS AND ALL INELME SOLUTIONS
CONCENTRATION CONTROL (VISCOSITY AND TEMPERATURE) WITH REAL-TIME DISPLAY OF EACH VARIABLE
IT CAN BE UPDATED AFTER THE FIRST INSTALLATION BY ADDING NEW FEATURES, ALREADY EXISTING OR FUTURE DEVELOPMENTS
CONFIGURABLE FOR ANY MODEL OF FLEXOGRAPHIC, ROTOGRAVURE, CARDBOARD PRINTER AND EVEN IN SPECIAL APPLICATIONS
DATA COLLECTION AND MEASUREMENTS OF TEMPERATURE AND VISCOSITY FOR USE IN FUTURE WORK
THE SOLUTION CAN BE INSTALLED WITH ALL MODULES OR WITH ANY OTHER COMBINATION THAT IS NECESSARY
ADVANTAGES THAT WE OFFER YOU AT INELME FOR THE CONTROL AND CONCENTRATION OF INKS
Traditionally, viscosity has been the variable used by printers to maintain colour in flexographic and gravure printing. As a result of our obsession with improving and innovating in each process, at Inelme we questioned whether viscosity was the only factor that influenced colour. And we found the key: temperature. It was then that we developed I-ICS, which adds to viscosity the control of ink temperature, thus calculating the concentration of solids and guaranteeing a homogeneous colour throughout the entire run.
- Goo
- Temperature control only
- Temperature control with plastic pumps with manual control
- Degradable plastic unit of measurement
- Measurement by sphere fall time
- Parallel installation
- Dialog terminal out of memory
- Measurement of ink concentration (viscosity and temperature)
- Measurement of ink concentration (viscosity and temperature)Measurement of ink concentration (viscosity and temperature)
- Temperature control with electronically controlled pneumatic pumps
- High durability and chemical resistance measurement unit
- Measurement by dart fall time
- Series or parallel installation
- PLC + PC with job storage software
DO YOU WANT MORE INFORMATION ABOUT THE INK CONCENTRATION CONTROL SYSTEM?